
October 1, 2012

Hello, I have a .22 that I recently aquired. Good, as it was fired a couple times in the 70s and then in the safe.Bad , I cannot loosen the allen screw between the cylinder and trigger. I have used break free and warmed it a bit with hairdryer. The head is not rounded yet but it isnt tight either. The bluing on this gun is UNBELIEVABLE which causes great concern about a lot of heat. How much can it take . Any one have ideas ? Also, I donated funds several weeks ago as I am a Dan fan since 1980. I think this site is great. Is there any way I can see if they got to the site? Thanks.... Hugelk

Range Officer

Range Officers

Dans Club
March 27, 2009

If I missed your first post a Big Welcome!
Now for the screws are these the side plate screws? Try an allen wrench and tap on it as you turn it see if you can break it loose! I haven't had trouble with those crews!
On the support, Jody would be the point of contact on this! Send him a PM on the site and he will check it! Not sure any one else has the ability to check the donations.
Keep us posted and show us that Dan!!!!

Supporter

Moderators

Dans Club
February 22, 2009

First, Welcome.
Try a soldering iron to the screw head. Heat and let it cool once or twice. That should cause the metal to expand and contract to break it lose. If that doesn't work, someone may have used lock-tight. Happened to me once and I broke the head off. Had to drill and tap...
Best Regards, Ron
Technically, the glass is always full; half liquid, half air....

October 1, 2012

Thanks a lot for the good ideas and warm welcome guys. It is a side plate screw. I am a pretty good McGyver and will proceed with caution. If this doesnt work as last resort I'll take it to my local smith. $75 an hour isnt easy to take.Hes pretty good.. but messing up a nice DW would be a lot worse. I am putting in a wollf spring kit and plan on doing the "poor man action job" at same time. Hugelk

Supporter

Moderators
January 24, 2009

In addition to the previous ideas, you may also try this. Grind the end of your allen wrench down a little, so you're sure you have the full 1/16" size you're working with (I think that's the correct size). The hex shoulders on the allen wrench can become rounded over time, allowing for more slippage.
If it still feels a little loose, put a small amount of valve lapping compound in the screw hole, then use the allen wrench. The compound will take up any extra space between the screw & wrench. If you don't have lapping compound, you could use some fine sand or dirt with a dab of oil. Just make sure you leave enough empty space in the screw hole to get your allen wrench in as far as it will go, so you get the best bite on it.
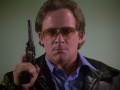
February 11, 2010

If it's a one shot deal, (you got one chance to get this right) I would use one of the
sockets that have the allenheads in them, insert and tap sharply a few times before
you try to turn. This has helped me on other projects. Also I would shoot a bunch
of PB blaster around and down the screw for a day or two before I tried anything.
-Blacktop

October 1, 2012

I really appreciate the ideas. I am going to do a combination of all , PB first for 2 days, tap a few times, use the soldering iron to heat and cool, and then either go the lap compound route or possible dremel down a larger allen wrench to conform perfectly with the " marginal" allen srew head hole. I will let you know how it turns out. Thanks again
Best regards, Hugelk


Dans Club
December 5, 2008

1 Guest(s)
